Feeling understaffed? Trying to increase production speed to make up for supply chain delays, or to become more competitive? Need to decrease waste but you’re not sure where to start? All of these conditions can lead to a stressed staff and higher turnover unless the mindset and tools of Continuous Improvement are applied.
WHAT TO EXPECT:
- Quick Changeover – Set Up Reduction Training
Reducing the time it takes for setups allows for more frequent changeovers and increases production flexibility. Smaller lot sizes, less scrap, shortened lead times and happier customers are frequent outcomes of Quick Changeover (aka SMED) training.
- Value Stream Mapping
Why is this tool to identify and remove / reduce “waste” in value streams so beloved? Don’t take our word for it. Lost Art Cultured Foods found time and improved quality. Downeast Coffee Roasters created a future map that guided their team to $1,500,000 in direct cost savings. Tanury Industries was better able to meet schedules and increased sales by 35%.
-
Process Flow Mapping
This type of map visually describes flow of work from customer order to generating and shipping work. With it you can identify redundancies and irrelevant processing steps that can be removed
- Spaghetti Diagramming
Extra steps are great for your Fitbit, not your production process … This tool helps teams see how parts and people “travel” through the shop. As National Marker Company’s Brandon Castaneda says, walking hundreds of feet and doubling back “adds up, and time is definitely money.”
WHO SHOULD ATTEND
- Production managers, Operations leads, plant managers, general managers
- Internal Lean Champions
- RI Manufacturing company presidents/founders/owners
ABOUT THE TRAINER
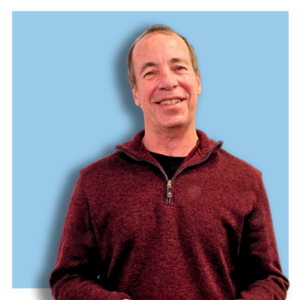