Company Profile
National Marker Company (NMC), a subsidiary of Justrite Safety Group, manufactures high-quality safety identification products. The Rhode Island company has been helping make the world “a little bit safer” since 1934. The company serves a variety of markets that require support with workplace safety, including the construction industry.
NMC’s portfolio includes signs, labels and tapes, hazard communications, facility products, COVID-19 pandemic signage and safety tags.
Situation
The company had experienced rapid sales growth by becoming an industry leader in product quality and lead times. To support this growth, operations in Rhode Island needed to be at peak efficiency, freeing financial resources, and physical capacity. This growth was achieved by investing in technology and talent, embracing Lean Manufacturing principles and tools.
Tags produced at the North Smithfield, RI, location made up roughly 15% of the NMC revenue on an annual basis. The team wanted to be ready to take on more work, however “we literally had machines scattered all over the production floor,” said Plant Manager Brandon Castaneda.
Associates walked hundreds of feet between equipment only to double back. “Probably 7 or 8 times throughout the day they had to make that trip back and forth. That adds up and time is definitely money.”
Internal leads and outside facilitators had run several small kaizens for the company, so they started creating spaghetti diagrams of the Tag Area. The complex nature of Tags had them creating more than a dozen different diagrams!
“We’re in a small building, and the company’s growing,” said Castaneda. “Even through the pandemic we’ve seen nothing but growth. Where are we going to put new machinery? Where are people going to work as we increase our workforce? Those were some of the things that we didn’t really have the answer to.”
Castaneda continued, “We knew that we probably could consolidate but how? That’s where Polaris MEP came in.”
IMPACTS
![]() |
Increased throughput in Tag area by 25% | |
![]() |
Sales increased 7% | |
![]() |
8% reduction in direct costs | |
![]() |
$25,000 unnecessary investments avoided | |
![]() |
5 jobs retained; 3 skilled workers re-assigned within the facility |
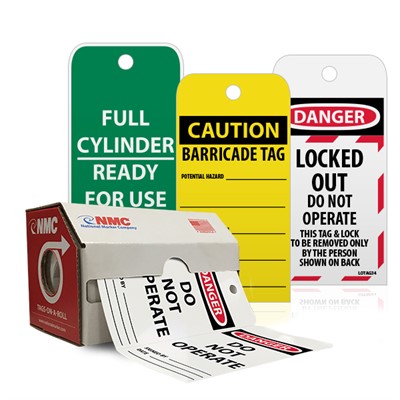
Polaris MEP is so well respected in the local community, and we have a lot of respect for the project managers and the team that are at Polaris. We’ve gotten comfortable with the group that’s there because of the results they have helped us achieve.
[Polaris MEP project managers] are fun, they’re energetic. They help us navigate some of the challenges in the kaizen event with the associate buy-in, with seeing it a different way, with not allowing preconceived ideas to hold us back. When we get to a point where we need to bring in an outside facilitator, Polaris MEP is always at the top of that list.
Andrew Ellison
Vice President of Operations, North America, National Marker Company
Solution
National Marker hired Polaris MEP to conduct a kaizen that ultimately would consolidate the Tag work areas. Kaizen is a term that refers to activities which continuously improve a business. In this case, the kaizen training event nearly came to a full-stop before it truly started for two reasons.
First, the complexity of Tag production. Project Manager Nathan Bonds quickly simplified the challenge by identifying the highest-volume workflow, which covered about 80% of Tag-related processes. “He jumped in and guided us down the right path,” said Andrew Ellison, Vice President of Operations, North America. “We can’t attack the entire thing so let’s focus in on that volume.”
Second, employee push-back. “We had associates who’d been doing things for a long time in a certain way and they felt that because they’d been working like that for so long, it must be the best way,” said Castaneda. Bonds approached the facilitation with Perseverance and Respect for People. Employees who had been against the effort “ended up being the biggest advocates of change afterwards.”
Results
“After doing the kaizen we were able to go from 4 or 5 dedicated associates in that area down to 2 dedicated associates,” said Ellison, “and our volume has not gone down. Our volume has only gone up since we’ve done this. Not only have we seen the growth, but we’ve also been able to reduce the cost of doing it. We’ve also added a lot of velocity in the lead time. We were able to improve our throughput by about 25% in the process while taking labor out of the work.”
The associates no longer needed in Tag production are now using their skills in other workflows which has expanded capacity for the company overall.
“We want to take what we’ve learned in tag manufacturing down to our Florida facility where the tag volume is about 3.5x the tag volume in Rhode Island,” said Ellison. “It’s an opportunity for us to take what we’ve learned with Polaris MEP and to scale it, to bring it life in another location where we’ll hopefully have even more benefits of cost reduction and improved customer lead times.”