The coronavirus means that many Rhode Island manufacturers are dealing with uncertainty right now ranging from a sharp decrease in business to the exact opposite. Keeping employees safe while at the same time keeping product lines running can easily overwhelm even the most seasoned management team.
How can companies be expected to handle an upcoming Quality Management Systems (QMS) audit with everything else they must balance?
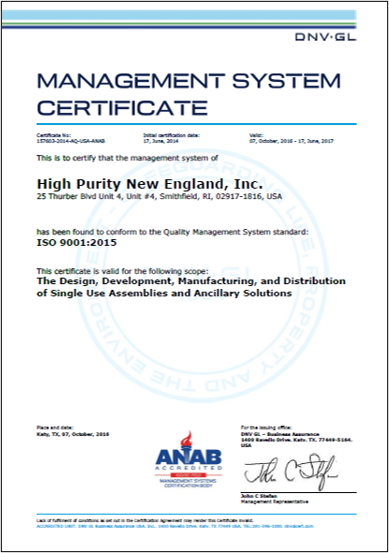
Why Should A Manufacturer Care About Certification During A Pandemic?
The Polaris MEP team has years of experience helping manufacturers ensure their systems comply with standards and technical certifications, whether those standards are imposed by customers or are regulatory requirements.
The same benefits that ISO or Nadcap or similar certifications offer in “normal” times – increasing employee performance, improving training outcomes, making production more consistent – will be advantages in the uncharted COVID-19 landscape.
QMS frameworks make the balance easier to achieve.
What To Do If Your Manufacturing Company Has an Audit Underway or Coming Soon
Here are three tips from the Polaris MEP team of auditors to help ease the strain of preparing for your next audit:
1. Communicate With Your Registrar
A “registrar” is an organization which can judge whether you’re satisfying the requirements of your ISO 9001:2015, AS9100 or other certification.
Many registrars are now offering remote audits (virtual audits) using technologies such as web meetings, document sharing and video streaming.
It can take some time and creativity to put these alternatives into place. Contact your registrar as early as possible to discuss alternative plans to your scheduled on-site audit.
In addition, your registrar should know the latest guidance from the governing bodies related to the coronavirus. Some, such as the ANSI National Accreditation Board (ANAB) support the use of information and communication technology for audits while also allowing certification bodies to extend expiring certifications in specific cases.
2. Hold A Management Review Meeting
Even if you’ve recently held a management review meeting for your QMS, begin reviewing any contingency plans your organization has and updating those based on what you’re currently experiencing.
This can help strengthen your QMS by documenting best practices as well as providing evidence of continual improvement of the system.
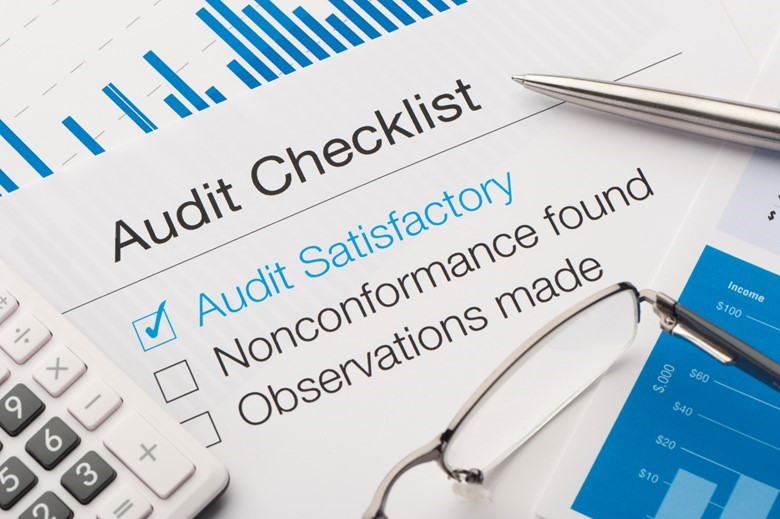
3. Conduct An Internal QMS Audit
If you haven’t already conducted an internal audit of your QMS, now really is a good time.
It’s a necessary component for the audit and is often put on the back burner by companies whose focus is elsewhere. If you’re not keeping up with it, the stress will compound come audit time. We can help!
Polaris MEP has a team of dedicated project managers who can help put you in the best compliance position possible. We can remotely audit your QMS using the same technologies as the registrars, which frees up your much-needed resources to keep focus on productivity.
Do you have a question about QMS compliance or audit preparation? Click here to email our Internal Audit lead, or call 401-270-8896.