Company Profile
Phil McCally was 10 years old in 1985 when his family purchased Lincoln, RI-based American Tool Company (ATC), a quality machining company with demonstrated expertise in turning, milling and drilling.
Originally founded in 1918, ATC has produced complex one-off parts for a wide variety of clients. Their primary market is capital equipment makers “100 miles from Lincoln.”
Situation
Like many who grew up in a manufacturing family, McCally was exposed to the business early on, sweeping the floor at 10 and working in production as a young adult. He secured a mechanical engineering degree and later left ATC for a few years to work at Rolls Royce Naval Marine. Working for this larger company at a higher tier in the Department of Defense (DoD) supply chain, McCally saw which suppliers were doing the best work.
“The shops all had ISO and some other qualifications. So, I felt the first step American Tool Company should take was to get ISO certified, not only to make us more competitive for DoD work but also to make us more crisp as an organization. The Quality team could communicate better with customers and with the shop floor.”
McCally also knew that “ISO isn’t just about me. Lean isn’t just me. The whole team has to believe in it. The whole team has to work at it to be successful.” To make the effort work, American Tool connected with Polaris MEP Project Manager Chris Cinieri.
IMPACTS
![]() |
Cost savings of $150,000 | |
![]() |
15 jobs retained, 3 skilled worker jobs added | |
![]() |
Investments of $120,000 in plant improvements and equipment | |
![]() |
Investment of $30,000 in new processes |
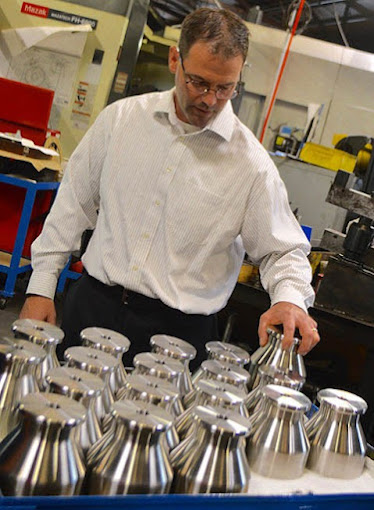
Solution
Cinieri said the ATC team had several key elements in place to make the effort successful:
• Their quality management system (QMS) was pretty close to the ISO standard; it needed more thorough documentation, not to be created from scratch.
• Employee culture was one of teamwork and improvement.
• Leadership (McCally) was committed to the training.
• It wasn’t going to be a “one and done,” but rather a comprehensive ISO plus Lean approach.
A Gap Analysis identified areas that would need to be addressed for ISO 9001:2015 certification. Cinieri worked together with ATC leadership to help fill those gaps and provided training to the entire ATC team prior to their audit.
“Chris came in for almost a year, getting us ready for the first audit,” said McCally. “He became one of us. He was integrated with the machinists and quality control. Chris really went through the whole organization from soup to nuts.”
Polaris MEP helped American Tool secure grant funding from the State of Rhode Island for employee training in Quality, Lean principles and 5S. This freed up time and money to invest in other improvements, such as an electronic visual metrics board on the production floor, a new Lean layout for the quality control area, and an employee training matrix.
Results
American Tool Company passed their ISO 9001:2015 Certification Audit on their first attempt with only a few, easily correctable “minors.”
Every part of the organization has benefited from the combination of ISO and Lean training, said McCally.
• Unexpected sales expansion. “It opened up the doors for a couple of business opportunities. We’re now doing more and more work with medical firm that we wouldn’t have gotten without ISO.”
• Greater efficiency. “It helped us get focused us on any trouble areas. If there’s a problem, like ‘Why did this same machining operation have an issue several months in a row?’ we can focus in and fix it faster.”
• Supply chain relationships improved and became stronger as reports more precisely document the work and any non-compliance issues with ATC’s suppliers. “Our long-term customers noticed the difference right away, that we are dealing with problems as they arise in a professional way. Suppliers realized they really needed to be on the ball.”
• Employee advancement. A team member who occasionally did quality control was promoted to Quality Control Manager. He led ATC through its second audit, which they passed with flying colors.
Even human resources benefited. ISO and Lean led to thorough and better documented procedures such as an employee matrix. This in turn led to easier onboarding and better organized ongoing employee training.
“Chris Cinieri is outstanding and we can’t say enough good things about him and the work he did,” said McCally. “I know that our organization is stronger and flows a lot smoother” since working with Cinieri and Polaris MEP.