Company Profile
igus, Inc. is a global company, headquartered in Germany, with a newly designed, 162,000-square-foot factory and office-space facility in East Providence, RI. igus has served the North American market for almost 30 years.
Products include innovative polymer bearings and chains – the plastic parts that enable movement in machines. It sells across many trades, including agriculture, construction and the automotive industry. igus’ rapid order shipment keeps their customers making money by minimizing machine downtime.
Situation
The company was efficiently fulfilling large orders on a regular basis, but the economic downturn of 2008 resulted in significantly smaller orders, and necessitated a change in business operations. igus realized they needed to improve their factory efficiency to survive in this changing environment. Improving their ability to handle any size order helped igus excel against their larger (and slower) competitors.
IMPACTS
![]() |
96% of orders ship in 24 hours | |
![]() |
Reduced customer complaints by 50% | |
![]() |
Transformed operations to efficiently process small orders |
“At igus we keep our customer’s machines up and running by ensuring rapid product delivery. Our lean processes and components inventory enable 96% order shipment within 24 hours”
Richard Abbate, Vice President
Solution
The Polaris MEP team helped igus transform their operations from a small, disorganized warehouse to the lean machine it is today. All igus employees, including the owner, take part in Lean 101 training sessions. The owner’s presence and attention demonstrated the high value assigned to the training by the company.
Lean processes have simplified and improved the consistent flow of an order from the customer all the way through packaging and shipping. igus now integrates lean skills and practices into ordering and stocking procedures, the manufacturing floor, and back into research and development.
Polaris MEP Project Managers were embedded in the igus transformation as they introduced lean practices to streamline all paperwork associated with orders, workspace standardization and daily quality checklists. The company has since eliminated phone calls to the manufacturing floor by using a system of instant messages via computers. All messages, instructions and installation notes are kept together and intact as they travel down the assembly line. This results in fewer errors.
Key to igus’ success is its adoption of lean practices throughout the East Providence facility.
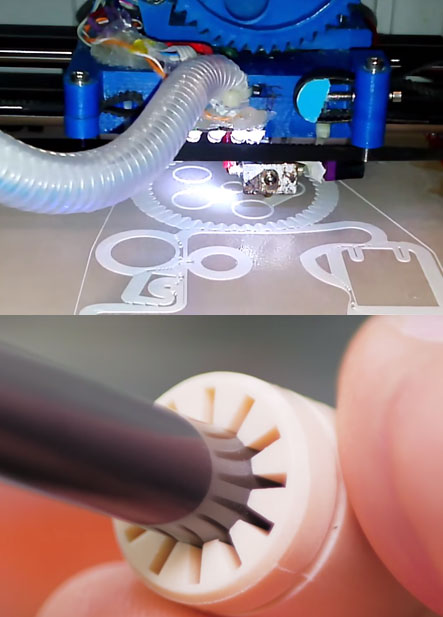