Company Profile
Hope Global, Inc. develops, markets and manufactures engineered textile components for high potential commercial and industrial customers. They continue to grow by leveraging their capability to provide value added solutions and outstanding customer service through utilization of their broad range of textile technologies and capacities.
Situation
Hope Global hired Polaris MEP to help them design and merge their two facilities, located in Cumberland, RI.
Polaris MEP’s Project Manager Carl Dwinnells worked with the Hope Global team to evaluate the current equipment and process flows, and setup the newly merged facility. This merge was to consolidate two facilities in Rhode Island for ease of operations and continuity of products and services.
IMPACTS
![]() |
$500,000 in facility cost savings | |
![]() |
Lean manufacturing process implementation to make the company more efficient | |
![]() |
Savings of 100,000 sq. ft. in overall floorspace |
“Without (the Polaris MEP Project Manager) we wouldn’t have been able to deliver the project on time and within budget.”
Paul Berlam, Vice President of Corporate Operations
Solution
The first steps in the process were to develop a Project Schedule to identify all the steps needed for an in-depth evaluation. This allowed for the identification of resources needed as well as the development of initial layouts to examine the feasibility of the project.
Cost, estimates and quotes from contractors were developed and a completed project plan was presented to the Hope Global management team. The merged facility layouts included new lean technologies that assisted in reducing costs in the future.
Layouts were designed with lean manufacturing tools and methodologies enabling a cellular flow environment. Creation of Kanbans and the implementation of 5S practices rounded out the project.
The original plan was to focus on only one section of the 250,000 sq. ft. building, however as time went on and business plans changed, almost all of the facility was affected. The project included receiving, manufacturing—assembly, loop, wire knitting, warehousing, offices and shipping departments.
The planning and construction of this facility were done with the coordination of both in-house facilities personnel, outside electrical contractors and other support services. Fire Riser and Evacuation plans were updated to satisfy local code requirements.
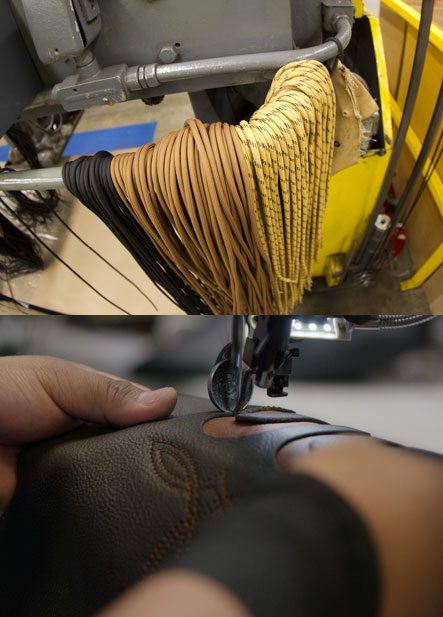