Situation
Chet Sutphen, President of Neocorp writes:
“Neocorp manufactures a diverse and growing range of custom and common use cordage, gaskets and stretch cord products at its factory in Rhode Island. Our competent work force, coupled with our unusually high-speed patented production technology enables us to ensure quick turn around and affordable, quality consistent products and solutions.
“Our diverse markets range from select sporting goods retailers to commercial fishing dealers to a variety of OEMS in North America and abroad. Neocorp produces over fifteen hundred stocked and made to order items with many shipping within three days. Stocked goods orders can be as small as $50.00 and made to order runs as little as $300.00.
“Over the years, Neocorp’s traditional marketplace and associated products have been heavily eroded due the changing external environment brought on by continued globalization. Our survival, to this point, has been based on our ability to grow a broader product offering and offering our products to a more diverse marketplace. We offer our products and services with competitively superior delivery times, quality and price points.
“The costs associated with this approach have been high, at times even self defeating. Inventory and cash flow were fast becoming the casualties of maintaining our service oriented market position. We re-visited our standard delivery expectations and were able to favorably modify them to some degree. We cross trained our production personnel adding to our flexibility. We trained our leadership team internally on decision making by functional area, established metrics by functional area and deemed obsolete a fair portion of our inventory. While these efforts yielded better control and some improvement, still more improvement was needed, particularly in the face of a weakening economy.”
IMPACTS
![]() |
Reduced inventory costs by 10% and space required by over 15% | |
![]() |
Increased capacity by 4 hours a week |
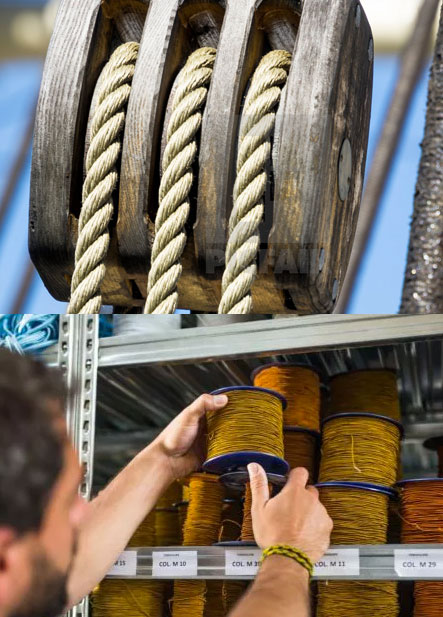
“With expert instruction from the folks at Polaris MEP and our focus centered on our mission and values, Neocorp has begun its continuous improvement journey. The Neocorp team has already seen benefits to our bottom line and our workforce. The highest costs associated with Lean are only those of ego and old habits.”
Chet Sutphen, President
Solution
Sutphen continues:
“Neocorp reviewed its situation with members of Polaris MEP (formerly RIMES). An assessment was conducted yielding a score card that showed areas we could improve in.
“Taking advantage of the nominal costs associated with Lean training programs and the potential value of applying those tools to our operation made the decision easy. We began with Lean 101 which gave us some concepts, definitions and fostered a focused team continuous improvement effort. That training was followed by Value Stream Mapping.
“Once our group became comfortable with Value Stream Mapping, we applied the tool to a popular Neocorp item, starting at production receipt of order all the way through to shipping. We determined that we did not need to produce and hold as much product as we did in work in process and sub-assembly.
“The ripple effect of this realization on inventory, cash flow and set-ups was clearly and immediately evident. Applicability of these same analysis tools are, and will continue to be, applied to other products and process to determine where time, effort and energy is being squandered. We have now begun 5S training for both shifts of our manufacturing employees.
While we are still in our 5S infancy, we have already received value extensions upon our value stream mapping training. Our recent Lean initiative has provided Neocorp with an enhanced formal platform of view points and measurements from which we have positively impacted our efficiencies, value propositions and corporate values. The additional benefits of team building and functional area integration were realized after just two days.”