Company Profile
Scot Jones wanted to spark innovation, while Jacky Beshar had a vested interest in job creation. In 1992, the duo joined Groov-Pin, a full-service supplier of grooved pins, threaded inserts and precision-turned components used in commercial, military and aerospace applications.
Groov-Pin, founded in 1926, is the parent company of Smithfield, RI based Precision Turned Components.
Precision manufactures a family of brass and stainless steel precision hardware, fittings, and connectors that are used in telecommunications, fluid and gas control, and medical applications. The company operates a range of multi-spindle and single-spindle lathes and secondary machines to create pieces ranging in quantities from 500 to five million.
Situation
“Precision Turned Components operates in an incredibly competitive market,” said Vice President Jacky Beshar. So when the downturn of the telecommunication industry hit in 2001, manufacturers of precision hardware and connectors were dealt a hard blow.
Precision Turned Components was not immune to the telecommunications industry’s demise and along with its competitors suffered a downturn. It took some time before the telecommunications industry began to recover, and when the market did recover customer orders did not stay in the U.S. Many orders were instead sent overseas to China.
“We felt the pinch. Increasingly, the less difficult jobs were sent to China and the more challenging work remained. And the jobs that did come back–came back harder to do, lead times were shorter and the quantities were smaller. It was a triple whammy all the way around,” said Beshar.
Precision’s machines were used to running 50,000 to 2,000,000 pieces at a time. “In the old days, when material was not expensive, labor was not expensive and customers were willing to wait, we could run the entire job at once even if the customer did not want all the parts at once,” said Beshar. “Now, jobs are harder, quantities are smaller and customers want it more quickly.”
Precision’s executives visited China many times to consider their options, and chose not to outsource the work there. “It is not why we got into manufacturing,” said Beshar. “We got into manufacturing to create American jobs.”
IMPACTS
![]() |
20% increase in profitability | |
![]() |
Machine set-up time reduced by 14 hours | |
![]() |
Dramatically decreased wasted movement of the segment of the products it ships, decreasing lead time |
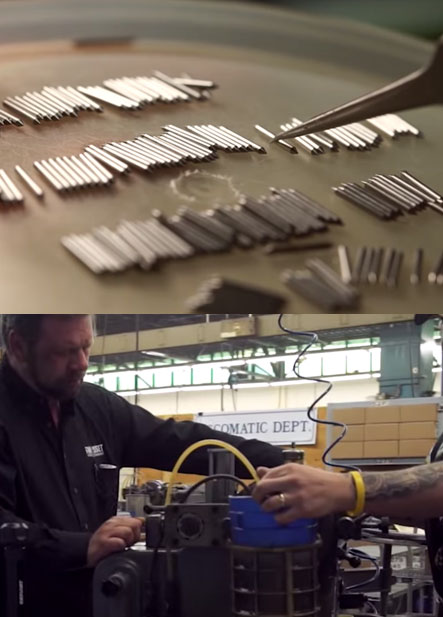
“Polaris MEP has provided us with a road map of how we can continue to improve everyday. We realize that it is a race without a finish line”.
Jacky Beshar, Vice President
Solution
Executives at Precision had an idea and decided that the best way to compete against China for jobs was to provide shorter lead times for customers. “If we could complete orders in less than four weeks we could better compete with China,” said Beshar.
Precision put in a new computer system to better understand costs and inventory and to have better control of managing the company. “The information taught us we needed a formal program to reduce set up times and lead times to make 10,000 pieces at a time instead of a quarter of a million and to do it in four weeks,” said Beshar.
That is when Polaris MEP came in. Polaris MEP started a Lean manufacturing process, funded in part by a grant from the Rhode Island Economic Development Corporation.
Polaris MEP encouraged Precision to start by implementing a 5S system. The system includes sorting, setting in order, shining, standardizing, and sustaining. “In other words, throw out what you do not need, make one place for everything, shine it up and fix the problems, standardize how everything is supposed to work and sustain the new system by auditing so that everything remains neat and organized,” said Beshar.
“We don’t sell tools, we build systems,” said Don Nester, Project Manager at Polaris MEP and consultant to Precision. Precision implemented the plan in the Cleaning Department where the 5S Team looked at reducing non value-added waste. Rather than clean each component at each stage of process, operators would do a light cleaning in order to move the process along more efficiently.
Precision also implemented a Lean Manufacturing Single Minute Exchange of Die (SMED) reduction system, a theory and technique for performing setup operations in less time. One of the key ingredients of the success of Lean Manufacturing is having strong commitment from top management. Top management in Precision’s case is five people and two of the company’s top managers sit on a seven-member steering committee with a Polaris MEP consultant. Each member of the steering committee is a liaison to one of the four core teams.