Company Profile
Spectrum Thermal Processing serves the aerospace, automotive, electronic, medical, and machine tool industries with specialty heat treating and brazing capabilities. The facility is ISO 9001:2015 and AS9100 Rev. D registered and Nadcap AS7003 certified. They provide a broad range of customers with vacuum brazing, vacuum oil quenching, surface enhancement including low-pressure vacuum carburizing and gas nitriding, and more.
Situation
Management wanted to improve communication between themselves and employees, between co-workers, between shifts, and ultimately between the company and their customers.Even though Spectrum Thermal Processing had achieved special accreditations and produced high-quality products, management knew there was room to improve their ability to efficiently process the wide range of jobs passing through their shop each day.
There were a number of factors that might have affected their process efficiency:
- The company serves many customers with parts sizes and lots sizes from 0.1 to 1000 lbs.
- Down time between process steps and damage to parts from handling add time and cost to a high percentage of jobs moving through the plant.
- Parts are bulk loaded, fixtured horizontally or vertically or sometimes supplied in fixtures for processing.
- Often there are multiple steps to the heat treatment process and parts are handled several times in order to get them to fit into the next furnace.
- Some furnaces have rectangular shapes and some are cylindrical. Basket designs must accommodate this.
Space consideration was also a challenge given the need to save packaging the parts arrived in to re-use for shipping back to the customer following treatment. There had been problems maintaining the shipping containers and packaging in good condition for return shipment.
IMPACTS
![]() |
$4,000 in savings per month | |
![]() |
Furnace capacity increased by 25% | |
![]() |
Reduced downtime | |
![]() |
Increase in employee enthusiasm |
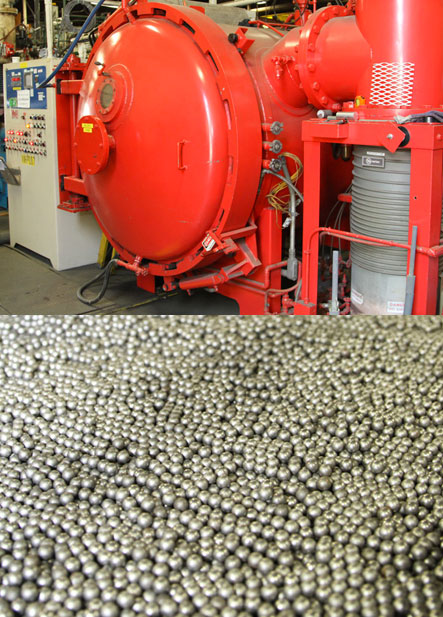
“In one case, employees identified a way to reduce load to load turnaround time from one hour to five minutes, allowing the furnace to process one extra load in the two shift operation and creating a 25% increase in capacity.”
Steve Egan,
General Manager
Solution
Use 5S principles of Sort, Set in Order, Shine, Standardize and Sustain as communication vehicle to improve operations and instill a “passion of ownership” throughout the business.
Spectrum Thermal Processing brought in Polaris MEP project managers to work at all levels in the organization to develop a more uniform materials handling system, minimize time between steps in the process and reduce damage from mishandling parts. Following the 5S principles, teams began using charts posted at each furnace to increase “value-add” time.
“In one case”, said Steve Egan, General Manager at Spectrum, “employees identified a way to reduce load to load turnaround time from one hour to five minutes, allowing the furnace to process one extra load in the two shift operation and creating a 25% increase in capacity.”
Polaris MEP staff also assisted teams with producing “spaghetti diagrams” showing parts “travel” through the shop, which highlighted the opportunity to move the lab and shipping areas together, eliminate steps, and open up space for much needed additional shelving.
Among the lean manufacturing changes implemented, the team concentrated the production of five furnaces into three which resulted in significant savings. Eliminating these two furnaces also created space on the shop floor for other operations and for shelving to hold original packaging materials until completed orders could be repackaged for delivery.