Company Profile
Technical innovation and quality products have always been at the core of Teknor Apex Company, an international custom compounder of advanced polymer materials. The Pawtucket, RI-based company started as a tire sales and recapping business in the early 1920s and has since transitioned its business several times to reflect economic changes and market demand.
Founded in 1924 as Apex Tire Company the business quickly transitioned from selling and recapping tires to mixing and supplying rubber compound to be used in shoe soles and wire insulation. Before long, the company also added garden hoses to its list of offerings and became the largest producer of consumer garden hoses. By the late 1940s, the company added vinyl materials in its offerings to be used in a wide range of applications from wire and cable to automotive, consumer, medical and industrial products.
The 1970s through to the Millennium brought a slew of changes and major growth. Teknor began opening additional plants in South Carolina, Vermont, and Kentucky, to name a few. Teknor Apex now has seven business units producing advanced polymer materials focused on vinyl, thermoplastic elastomers, engineered thermoplastics, bioplastics and colorants; manufacturing facilities in nine locations in the U.S. and three in Singapore, the United Kingdom and China; and 1,800 employees.
Situation
Things, however, have shifted for Teknor Apex since the two key drivers behind the company’s business are the housing and automotive industries. “The common comment in the plant was if GM sells a car, we will make something,” said Teknor Apex’s Rhode Island Plant Manager, Chris ReCasino. “But both of those markets were absolutely depressed last year.”
Because the two industries were struck a hard blow from automotive business nearly going bankrupt and the housing market crashing, Teknor recognized it had to take a hard look at its business.
Teknor’s senior management team realized years ago that productivity gains were falling below expectationsand were seeking proven methods of continuous improvement. Management experimented with several methods, but the best one was Lean Manufacturing.
Executives recognized one of the major problems was a loss of productivity due to machine downtime. Downtime for manufacturers occurs when employees need to changeover the machine to manufacture a different product or to provide maintenance to the machine.
The goal was to increase productivity through reduced downtime and overall, reduce conversion costs. It was not, however, going to be an easy challenge.
IMPACTS
![]() |
$39,000 in cost savings due to decreased downtime | |
![]() |
changeover time decreased from four hours to 2.5 hours on average | |
![]() |
Physical Testing lab experienced a 10% increase in productivity and a 5% reduction in sample turnaround time |
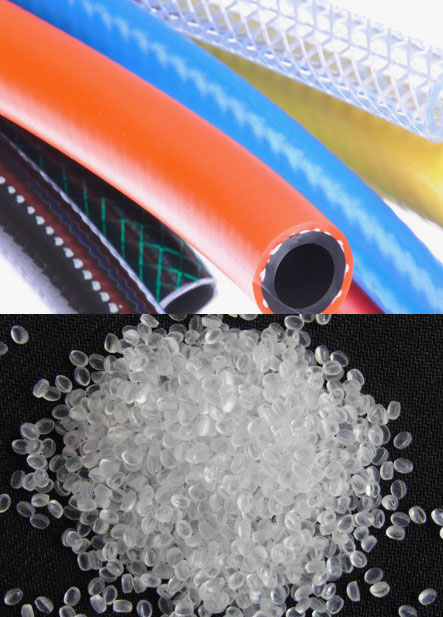
“They are all very professional people at (Polaris MEP),” ReCasino said. “Don Nester is the most familiar with our business because he came from a chemical business so there was an immediate buy in. He has been the essential piece in making sure we are using the same tools and being consistent.”
Chris ReCasino, Rhode Island Plant Manager
Solution
“We recognized we needed some help to put it all together and be more active in the use of outside resources,” ReCasino said. “Polaris MEP was selected because it was a state-supported program and one of our sister operations had success using (Polaris MEP) to introduce the principles of Lean Manufacturing into their plant operations.”
Polaris MEP was able to provide consulting services to Teknor because of its partnership with the Rhode Island Economic Development Corporation. The EDC provided some of the necessary grant funding for Polaris MEP’s services.
The Pawtucket steering team did its homework on what Polaris MEP had to offer in Lean Manufacturing, a system which helps a company produce more with existing resources by eliminating non-value added activities. Lean Manufacturing also establishes a systematic approach to eliminating waste and creating flow. One piece of Lean Manufacturing is the 5S System, a basic systematic approach to improve workplace organization, standardization and safety.
“After visiting our sister operation and a few other operations that utilized these principles, we were very enthusiastic about implementing it, but we did not know what would fit and what would not fit,” ReCasino said. “We had to be more creative and look at things from a rudimentary point of view.” Teknor implemented the 5S system of sorting, setting in order, shining, standardizing, and sustaining.
Polaris MEP consultant Don Nester and the Steering Team at Teknor put together four teams in just over a year in hopes of empowering employees to help get rid of non-value added waste and to create positive change. “(Polaris MEP) was one of the facilitators at the team meetings and they helped us assess our early stages of success or failure during steering committee meetings,” ReCasino said. “They helped us create the hands off management idea and let the machine operators and hourly employees make suggestions.”
Hearing what employees have to say is essential to any success, according to ReCasino. “The guys on the floor know how the machines work and operate better than I or even better than maintenance guys do.”
One of the biggest changes after implementing Polaris MEP’s system was in Teknor’s Maintenance Department. Before Polaris MEP came in Teknor’s Maintenance Department was located nearly 500 feet away from its manufacturing operation facility. “We were a fairly large operation at one time and it made sense at the time,” ReCasino said. “But maintenance should be in the heart of manufacturing.”
After assessing its location and using a “spaghetti diagram” to study their work patterns, the Maintenance Team recommended to management a relocation of some of the key maintenance operations. Executives were informed that it took 15 minutes of walking time to get to the site that required maintenance. Getting to the parts required an additional 15-minute walk back to the shop for parts and tools.
“Fifteen minutes per call and everybody gets a call every day and that is 20 people multiplied by 15 minutes results in four to five hours per day and that is just to go see what the problem is,” ReCasino said.