UPDATED August 26, 2020
By Polaris MEP Partner Josh Chernin, Business Improvement Group
During the economic stress caused by the pandemic, manufacturers must work harder to anticipate and reduce costs and supply risks BEFORE those elements are locked into a final product design.
Product design has two purposes.
- To create a useful product, with its own function, form, look and feel – the traditional definition of product design.
- To produce that product at the lowest possible cost – certainly at a cost the market will bear, and better yet, lower.
The second purpose is where Design for Manufacturing (DFM) comes in.
Designing for Manufacturing / Cost Considerations As Well As Functionality
By the time a product is fully designed, about 75 percent of the manufacturing costs are locked in. This is not only due to the functionality of the product, but also to the choice of materials and the manufacturing process.
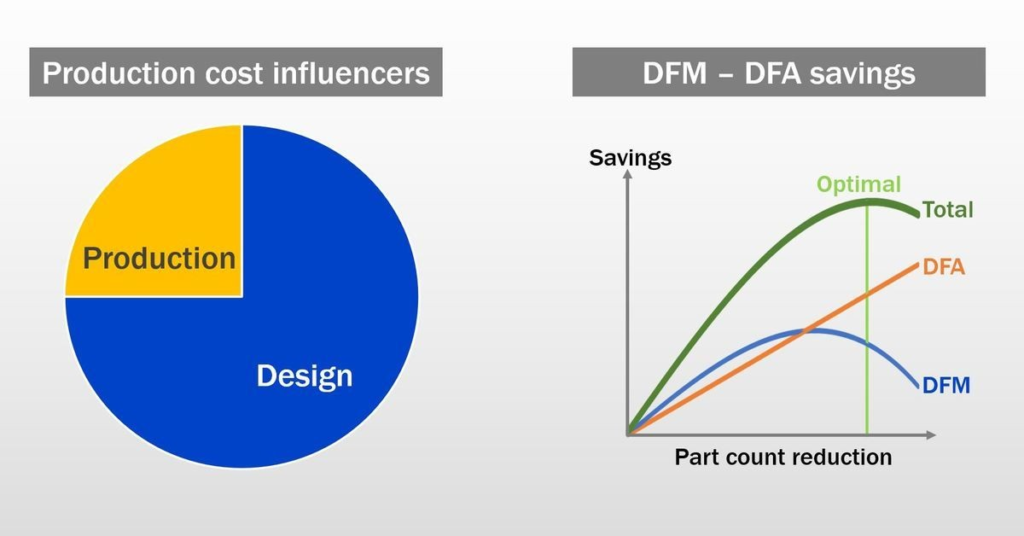
Done correctly, DFM performed in parallel with – and as part of – the traditional product design. This means that from the very beginning of the process, manufacturing and cost considerations are equally as important as functionality.
Costs must be reasonable (DFM) AND the product must be useful (traditional product design) or it won’t meet with success in the market.
Start With a Challenge, Break Down Walls
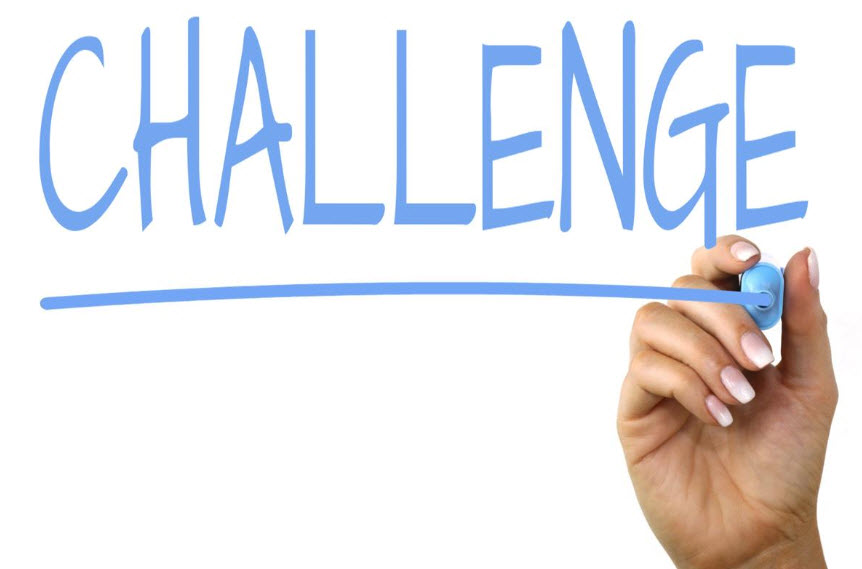
The process begins with a challenge statement – a response to the question, “What market need are we trying to meet?” It’s very important that this statement not be a solution statement.
For example, if the challenge is that “older people need bicycles that are easier to pedal,” that is the challenge statement – not “we need to produce an electric bicycle.” Electric bicycles are only one of many possible solutions to the challenge. There may be other, better solutions that are not considered by jumping immediately to electric bicycles.
The next step is to assemble a cross-functional design team comprised of traditional designers and folks with expertise in marketing, sales, finance, purchasing and manufacturing.
The old method of designing a product and throwing it over the wall to the other business departments in succession is over. That process will, in the end, take longer to get to the market and very likely cost more than necessary. The idea now is to make sure all the important questions and considerations are discussed at the beginning, before the actual designing takes place.
After agreeing on a challenge statement, the team needs to assess and list the features and functionality of the product to the customer. After that, it’s a push-and-pull, back-and-forth process for the team to optimize features, functionality and cost while keeping the targeted price point and volumes in mind.
It can be a messy, iterative process, but there are several tools and methods that bring order to the process. Work with an experienced team to find the right approach for your products.
The Perils of Over-Engineering
This summary doesn’t do justice to that process. That’s a subject for another day. But I will comment on one frequent error: Over-engineering and over-specifying.
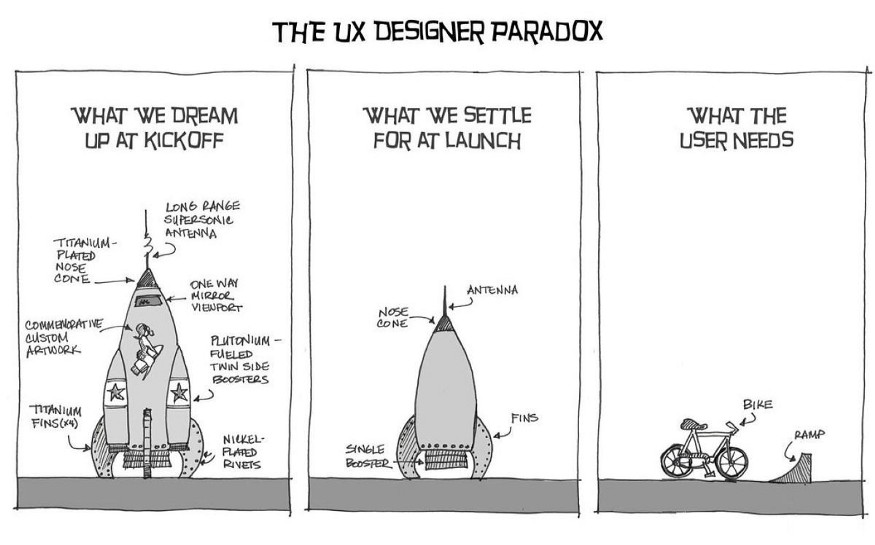
For example, it may be technically possible to hit a tolerance of .0001” on a part. But if that part requires a tolerance of only .001”, then specifying the more demanding tolerance only adds cost.
Similarly, tolerances that always don’t match each other – like the classic example of an airplane door and the opening for that door in the fusillage “overlapping” each other’s tolerances — will similarly lead to problems in manufacturing.
Design for manufacturing may seem slow, especially when the urgency to get a product into the market seems most important.
But it’s actually faster and less costly than designing a product in isolation, only to find out that the manufacturing cost is higher than it should be – or worse yet, that the product can’t be made at a price acceptable to the market.
Josh Chernin is a partner with Business Improvement Group LLC. Interested in process improvement or having a consultation with Polaris MEP resource partner Josh Chernin? Contact Kayla Viveiros at Polaris MEP, kviveiros@polarismep.org.