Better Product, Better Results
No manufacturer sets out to have quality issues, but the reality is that, over time, quality and process controls can erode. And it often takes only a few mistakes to kick off a serious decline, wreaking havoc on your reputation and bottom line.
It’s impossible to obtain zero defects, but maximizing quality is always worthwhile. A reputation for producing quality products reliably and safely will lead to more sales, increased customer loyalty, and reduced waste and production costs.
These efforts can also help you obtain Quality Management System certifications needed to reach certain target markets or simply fulfill your customer’s rigorous requirements.
Seek quality and many things will fall into place.
Our facility provides products to Aerospace and other demanding Industries. Without Polaris MEP’s assistance with this certification and improved QMS, this business would be lost.
Royal Jones
Senior Quality Manager,
DeWAL/Rogers Corporation
Solutions To Your Challenges
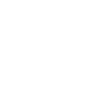
Lean Manufacturing
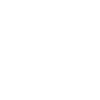
Quality Management Systems
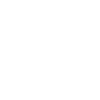
Facility Layout
How We Help

QMS PREP
Polaris MEP project managers can guide your team, step-by-step, through the preparation process for any QMS audit. Whether for ISO 9001:2015, ISO 13485, ISO 14001, AS9100D, or another QMS, we’ll uncover compliance gaps and get you in the best possible position before your audits.

CONTINUOUS IMPROVEMENT
A Polaris MEP Lean expert can help your team begin (or continue) a Lean journey through a culture of continuous improvement. This new approach can help your team increase quality in all aspects of their work.

360° ASSESSMENT
The issues impacting quality can sometimes be hidden from view. By analyzing your company comprehensively, from all angles, we can identify points of failure and find ways to refine processes to maximize the quality of your output.

PUBLIC TRAINING
Polaris MEP provides a variety of workshops, lunch & learns, bus tours, and more to help keep your team informed on best practices. The more people that understand the factors impacting quality, the more likely your team will find ways to improve on their own.
Spotlight On Quality
- Earn and secure a reputation for reliability and safety
- Increase sales through new markets that require QMS certification
- Instill a culture of quality and continuous improvement in your team
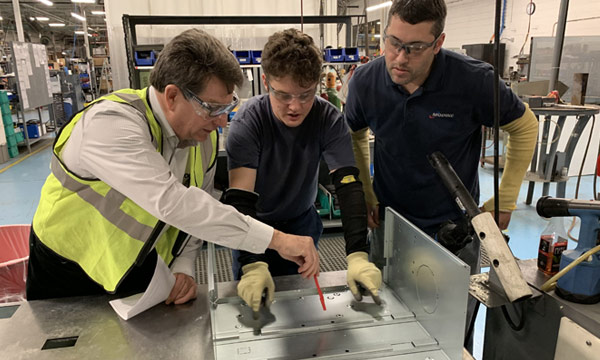
Related
MEP Facility Layout Services Help MOO, Inc. Enjoy Cost Savings and Greater Efficiency
Company Profile MOO, Inc. was founded in the United Kingdom in 2006 with a mission of “shaking up the print industry” and offering beautifully designed, high-quality branded items ranging from business cards to notebooks. In 2009 MOO established a presence in the...
As Key Employees Near Retirement Age, Jade Manufacturing Turns to MEP Center to Educate and Empower Team
Company Profile Founded in 1945 by Arthur Boyle, Jade Manufacturing Company Inc has remained a family-owned business for three generations. President Chris Burch and Director of Manufacturing Steve Gruner are currently at the helm of the company which builds products...
Lean Inventory Training Helps Glassworks Studio Reduce Mess and Stress, Increase Success
Company Profile In 2004, artist Tracy Glover found that she was so busy with her “on the side” glassworks design and production, she quit her day job and founded her own studio. Pawtucket-based Tracy Glover Studio has since grown in size – 8 employees and a 5,000...
Polaris MEP was instrumental in our company achieving ISO 9001:2015 certification.
Dr. William Weedon
President/CEO, Applied Radar, Inc.
Where is your strategy driving your company?
Schedule your assessment today!
Please complete the form below and a member of our team will reach out within one business day.