During this time of COVID-19 social distancing, how do we continue safely manufacturing without a loss of productivity?
My expertise is facility planning – creating plant layouts that improve manufacturing productivity. In the past, I helped manufacturers decrease floor space. Lately, I am working with Polaris MEP clients to adjust spacing by creating a “Safety Zone” for each worker.
One of the lowest-cost solutions for the creation of safety zones is to set up work cells.
How Work Cells Work as “Productivity Zones”
When you have a work cell (sometimes spelled workcell) you collect all the people, equipment and supplies needed to perform a task in one location.
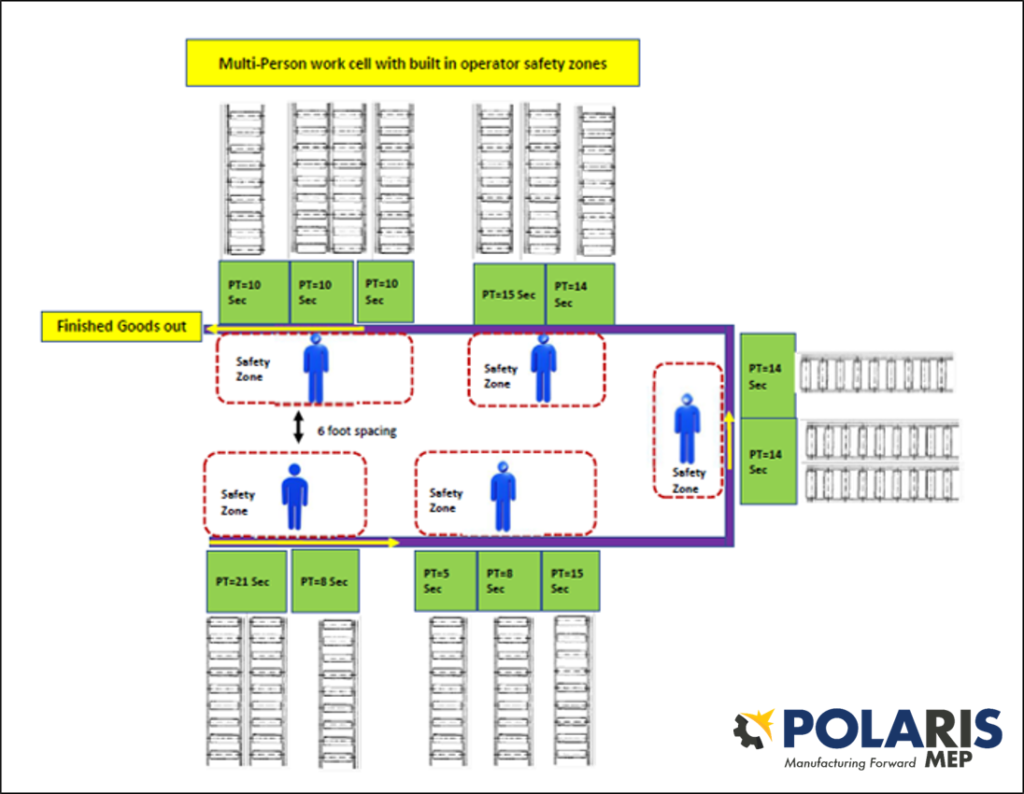
The work cell may consist of one or more people working together putting out product at the same rate as the customer demand. By matching the output to customer demand, the work cell is constantly running which increases productivity and eliminates large build-ups of finished goods inventory.
A work cell turns a work station into a “Productivity Zone.” Advantages of properly implemented work cells are reductions in:
- work in progress,
- material handling cost,
- material flow distance, and
- production lead time.
Work cells optimize lean manufacturing because employees
don’t waste time criss-crossing the plant floor for materials. Having employees
working next to each also increases communication and problem solving.
However, in our new COVID-19 reality,
manufacturers can’t have employees safely sitting next to each other. This is
where flexible facility planning can help.
Work cell “Productivity Zones” can be turned into “Safety Zones” which keep workers separated by the six-foot recommended space allowance.
How To Adapt Work Cells into “Safety Zones”
The first step is to calculate the customer Takt
Time. Takt Time is the average time you need to satisfy customer
demand.
It’s measured by the average time between the start of production of one unit and the start of production of the next unit, when these production starts are set to match the rate of customer demand. This is an important calculation in lean manufacturing:
Takt Time Formula = (Net Time Available for Production)/(Customer’s Daily Demand)
The result of the calculation is the number of seconds the operation must complete one unit to satisfy the customers demand.
For example, if the Takt Time is 85 seconds, the work cell process time is set up at or below 85 seconds. Let’s imagine that there are eight operations in a work cell, and each operation has a process time of 10 seconds. The overall process time in the work cell is then 80 seconds — below the customer Takt Time of 85 seconds.
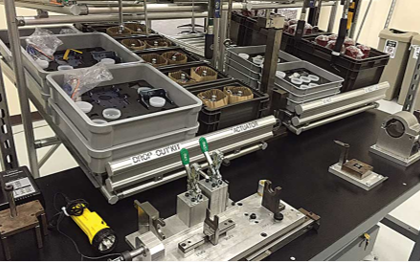
Once the operations in the work cell are determined, the next step is to set up the cell so only one operator is needed in the “Safety Zone.” The material the operator needs in the work cell is supplied from the rear by workers meeting state guidance for protective gear (masks or face coverings). The output from the work cell is sent out of the cell by using a roller conveyor (or powered conveyor).
There is now no reason for anyone else to enter the operator’s “Safety Zone.”
If for some reason operators must work close to each other, other precautions can be put in place such as plexiglass barriers.
Rear-Loaded Manufacturing Workstations Are Safe, Efficient
Example #1 : One Workcell that will satisfy the customer Takt Time of 85 seconds. Notice that all material is supplied from the outside of the cell which creates an Operator “Safety Zone.”
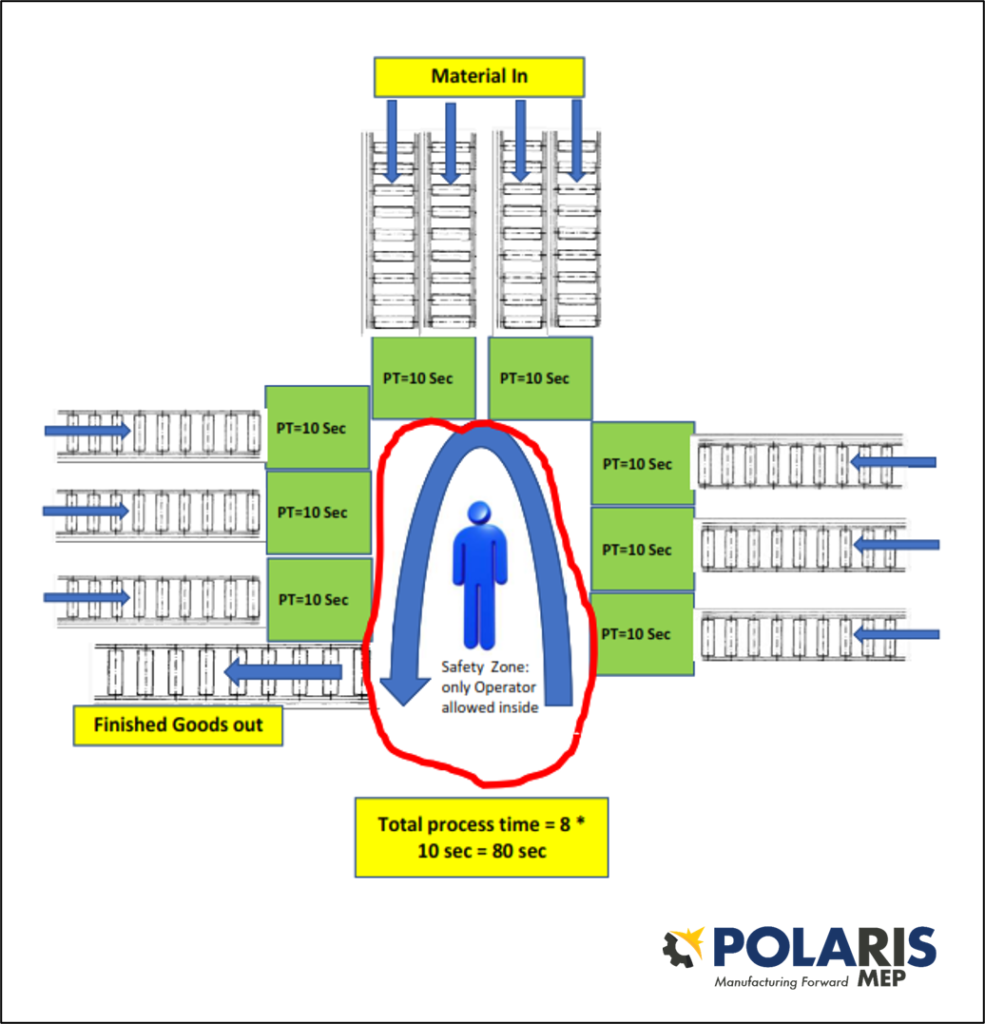
Example #2: If the customer Takt Time was 42.5 seconds, two separate work cells would be created with four operations in each one to satisfy the demand. A finished unit would exit the two cells every 40 seconds.
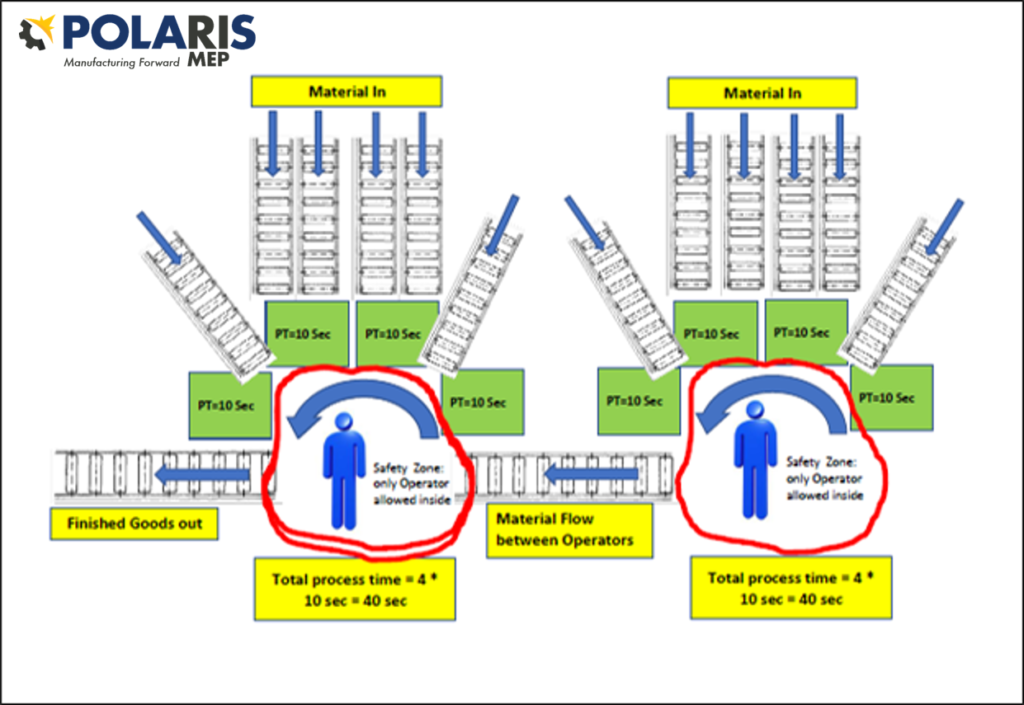
Notice that in example 2, the material is transported between the work cells using a roller conveyor. This will keep the operators from imposing on the others’ “Safety Zone.” In both examples, rear-loaded workstations ensure distance between the operator and other members of the team.
Converting work stations into flexible, rear-loaded work cells can increase productivity and keep the current recommended COVID-19 social distancing requirements.
Even when the current crisis is over, you will find that your facility planning investment will be a good return of your funds.
Need assistance re-engineering your workstations into flexible, productive “Safety Zones”? Contact Ted Kennedy at 401-270-8896 or tkennedy@polarismep.org.