Among the many issues over the last few years, two major human challenges have developed. Could cobots (collaborative robots) be the answer?
The first trend is the need to implement social distancing to slow the possible spread of the COVID virus and become more resilient should new viruses appear. The second major issue is labor shortages due to both low labor participation rates in the workforce and higher demand.
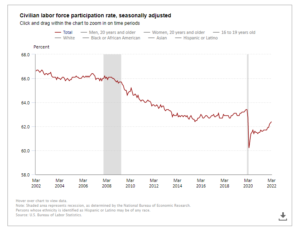
Civilian labor force participation rate chart via the U.S. Bureau of Labor Statistics.
The civilian labor force participation had been declining for many years, but there was a sudden drop during the COVID pandemic.
Labor force participation is on the way back up now, but it’s not at a healthy point. And manufacturing can’t just take anyone off the street. Most jobs require a basic level of skills or training.
Flexible automation solutions like “cobots” can help alleviate the issues with both of these challenges.
What Is a Cobot? How Does It Differ From Other Industrial Robots?
Typical industrial robots work on their own and fully take over a given task. Cobots are collaborative robots. They work with people, not in place of them.
Cobots create a hybrid work environment that improves efficiency and safety across a wide variety of industries and tasks. The cobot joints are more flexible, and the movement velocity is monitored by encoders. By this design cobots will stop immediately if they encounter an object that should not be in their path of motion.
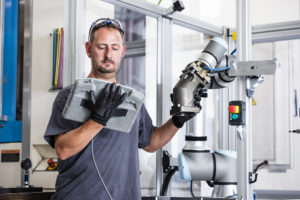
Image Source: Universal Robots
In other words, when a cobot is working next to a person, if it moves and encounters the person it will stop without hurting them. Most industrial robot do not have sensitive controls like that and will not stop unless there is a large opposing force.
Industrial robots need an enclosure build around them to make sure people cannot get into their work environment. Cobots do not need any protective enclosures around them. They are made to work with people.
Other main cobot features are their lower cost, light weight, and ease of programming. I have carried a small cobot easily in the past since some versions are only about 25 lbs. Cobot movement can be programed by putting it into “Teach Mode” and moving the arm and joints with your hand to where it should go — very simple to do.
Cobots can even be used to do multiple operations by putting them on a movable base that is wheeled to a workstation and locked in place. You move the robot to where it is needed most.
Cobots Can Improve Both Worker Social Distancing and Manpower Problems
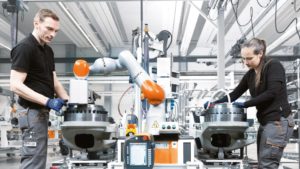
Image Source: EMag by Direct Industry
Since cobots are made to work alongside people, they can be strategically placed to provide better spacing between people. You locate the cobot between people, so they are taking parts from one person, doing an operation on the parts, then passing the completed parts to the next person. The cobot location and reach creates healthy distance between the people in the work cell.
Even the smallest manufacturer can use cobots to do repetitive work and lower your costs.
Ideal jobs for cobots are screw driving operations and machine tending — loading and unloading parts into equipment like presses, molding machine, and CNC machines. In these situations, people can line up the work for the cobot and take away the finished parts. The cobot’s function is to load and unload the parts to the equipment.
Using the cobot for some of the mundane work will free up the human for more complicated tasks. This reduces your manpower needs. And, your already-trained, already-skilled workers will be doing jobs of higher value and feel more satisfied.
In today’s tight labor market and with the need for continued social distancing cobots may be one of the best solutions. Due to their cost and the benefits, they can give you they are often economically feasible for deployment in production.
Polaris MEP can help you determine whether cobots and/or other automation solutions are right for your company. Book a call with Ted Kennedy to talk about Automation Readiness.